In B2B trade, the importance of inspection in quality control is paramount. The role it plays is crucial in maintaining quality, detecting defects, and ensuring compliance. Being a vital part of the supply chain, it acts as a safety measure to guarantee the authenticity of products and services, thereby promoting trust and confidence in business dealings.
Before we delve into the significance of inspection in quality control, it’s essential to understand its role in B2B trade and its transformation. In this article, we will examine how incorporating inspections into B2B trading platforms can transform the industry, increasing efficiency, transparency, and dependability.
Understanding the Importance of Inspection in Quality Control
The importance of inspection in quality control cannot be overstated. It refers to the systematic examination of goods or services to ensure they meet specified criteria. It is a critical component of quality management systems, designed to detect and rectify any deviations from the standards.
In the past, the process of quality control and inspection was done manually, which included physical checks and documentation. Any problems found could range from a machine part being misaligned to a crack in a ceramic vase. This process was very time-consuming and required a lot of attention to detail.Â
Nowadays, with the advancement of digital technology, automated quality control and inspection processes have been introduced. These modern techniques are more efficient and accurate, reducing the time taken for manual checks and minimizing the risk of human error.
Key Reasons for the Importance of Quality Inspection in B2B Trade
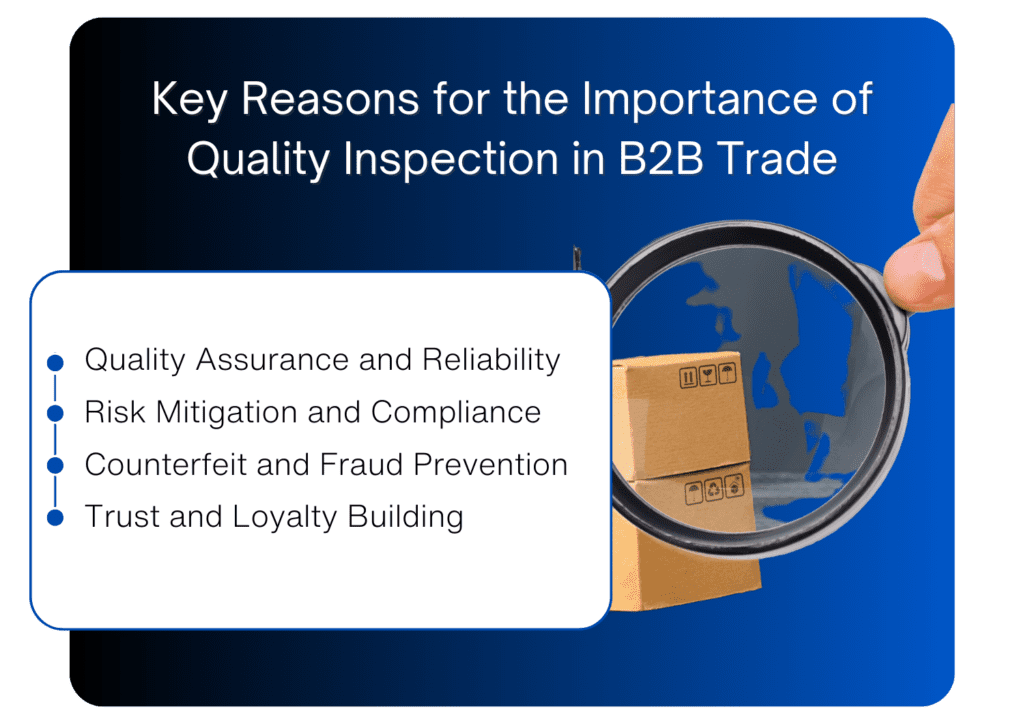
-
Ensuring Product Quality and Reliability
The promise of product quality and reliability is at the heart of B2B trade. Businesses must trust that the goods they're purchasing meet their expectations and the standards set out in their contracts.
Inspectors can identify defects or inconsistencies through meticulous examination, ensuring that the delivered goods meet the buyer's expectations. This not only ensures the quality of the product but also protects the seller's reputation. -
Detection and Prevention of Defects
Defects in products can be costly. They can lead to product recalls, damage a company's reputation, and legal action. Quality control inspection can detect these defects early in production, allowing for timely rectification. This prevents the circulation of defective products and saves costs.
-
Meeting Quality Standards and Expectations
In today's competitive market, meeting quality standards and expectations is more critical than ever. Traders demand high-quality products, and businesses that fail to deliver can quickly lose market share.
Quality control inspection helps businesses meet these demands. By verifying that products adhere to specified criteria, companies can assure their buyers of the product's quality, increasing satisfaction and loyalty. -
Minimizing Risks and Ensuring Compliance
The world of B2B trade is fraught with risks. Counterfeit or substandard products can slip through the cracks, leading to significant losses and potential legal issues. Quality control inspection aids in the identification of these products, thereby minimizing the risks associated with non-compliance.
Moreover, it ensures that businesses adhere to regulations and industry standards, avoiding potential legal repercussions and damage to their reputation.
-
Building Trust and Resolving Disputes
Trust is a crucial element in B2B trade. Buyers need to trust that their products meet their specifications and quality standards. Quality control inspection reports serve as a credible source of information, assuring buyers of the product's condition and quality.
These reports also play a crucial role in resolving disputes. They provide objective evidence to help settle disagreements regarding product quality or specifications, preventing costly and time-consuming legal battles.
Integrating Inspection within B2B Platforms
The integration of inspection within B2B platforms is a game-changer. It streamlines the procurement process, enhances transparency, traceability, and quality control, and makes inspection a core part of B2B platforms. This transformation is not just theoretical; it’s already happening.
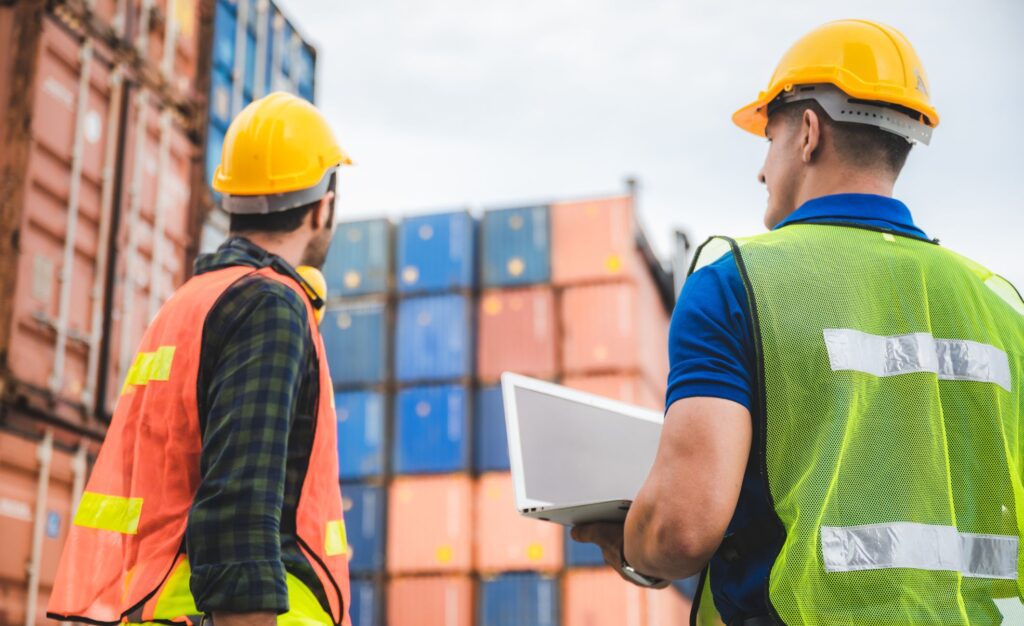
The Digital Technologies Driving Integration
This integration is powered by advanced digital technologies that are reshaping the landscape of quality control and inspection:- Machine Learning
Algorithms analyze data to identify patterns or anomalies, enhancing the accuracy of inspections
- Artificial Intelligence (AI)
AI automates the inspection process, reducing time and cost while improving accuracy
- Computer Vision
This technology analyzes images of products to identify defects, which is particularly useful in industries where products have a visual component
- Internet of Things (IoT)
IoT devices monitor and collect data on various aspects of the production process, helping to identify potential issues before they escalate
These technologies are not just theoretical; they’re being applied in real-world scenarios. Strategic partnerships in the industry among key players are leveraging these technologies to provide integrated solutions that streamline trade processes and ensure product quality and compliance.
Streamline your B2B trade processes and gain access to a large pool of qualified inspectors with Distichain.